Gas cabinets and panels for heat treatment plants
AVION and SCADA
Since 1996, AVION Europe’s field of activity has expanded enormously and, in addition to spare parts and services, increasingly includes complex tasks such as the design of gas mixing batteries, modernization of control systems (e.g. S 5 to S 7), control cabinet construction and the creation of complete SCADA systems according to individual customer requirements.
In the following, we explain our delivery options in these areas in bullet form. Prerequisite for all respective systems: Intensive consultation by our specialists with many years of experience in the heat treatment industry.
- Automatic control of carbon potential and atmospheric generation (nitrogen and methanol).
- Analog or digital flow meters for perfect measurement and control of gas consumption
- Custom design and build on customer preferred high quality components
- According to the current safety and industry standards
- Gas leak detection system with alarm
- Gas supply with:
- Propane or natural gas
- Nitrogen
- Air
- Endoatmosphere
- Methanol
- Ammonia
- other
Modernization or complete new construction of gas mixing and control stations or even measurement of atmospheric composition from a single source. As stationary systems with clocked measurements of several individual furnace systems or as a mobile solution for individual control measurements. The gas analysis devices of Supersystems Europe (SSI) are distributed in German-speaking countries exclusively by AVION Europe – service included.
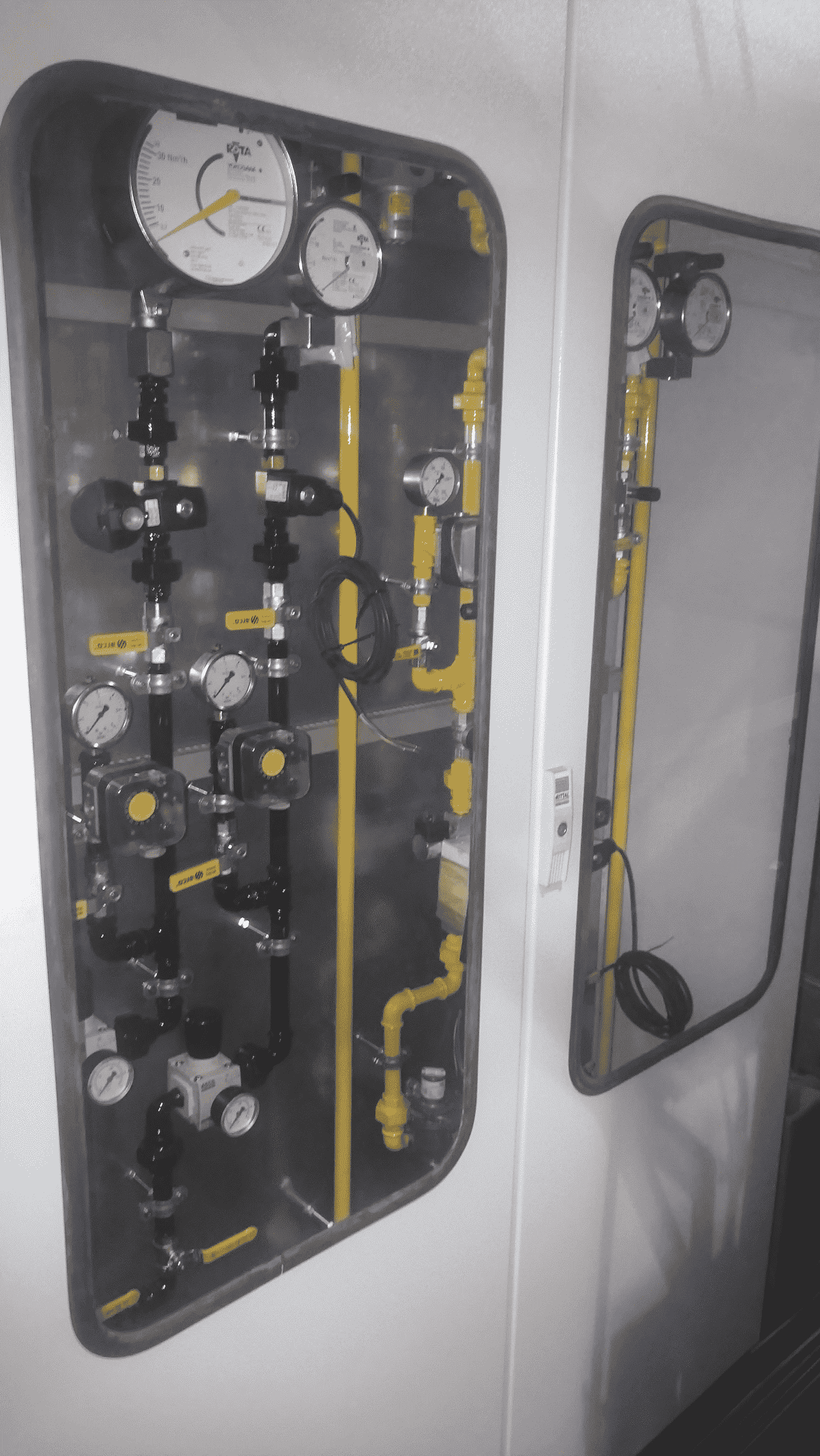
Automatic gas analysis
- Automatic 3 or 4 gas analyzers of the latest technology with single zone or multi-zone technology, integrated with control systems and gas flow regulation panels.
- Multi-zone analyzers for measuring up to 8 zones or separate furnaces one after the other, save money on investment and ensure very good measurement quality
- 3 Gas analyzers for measurement
CO, CO², CH4 - 4 Gas analyzers for measuring
CO, CO², CH4 and H² - Easy integration with existing PLC software to control, monitor and record carbon potential,
- Integrated systems ensure best product quality and process repeatability
- Complies with CQI-9 and AMS2750
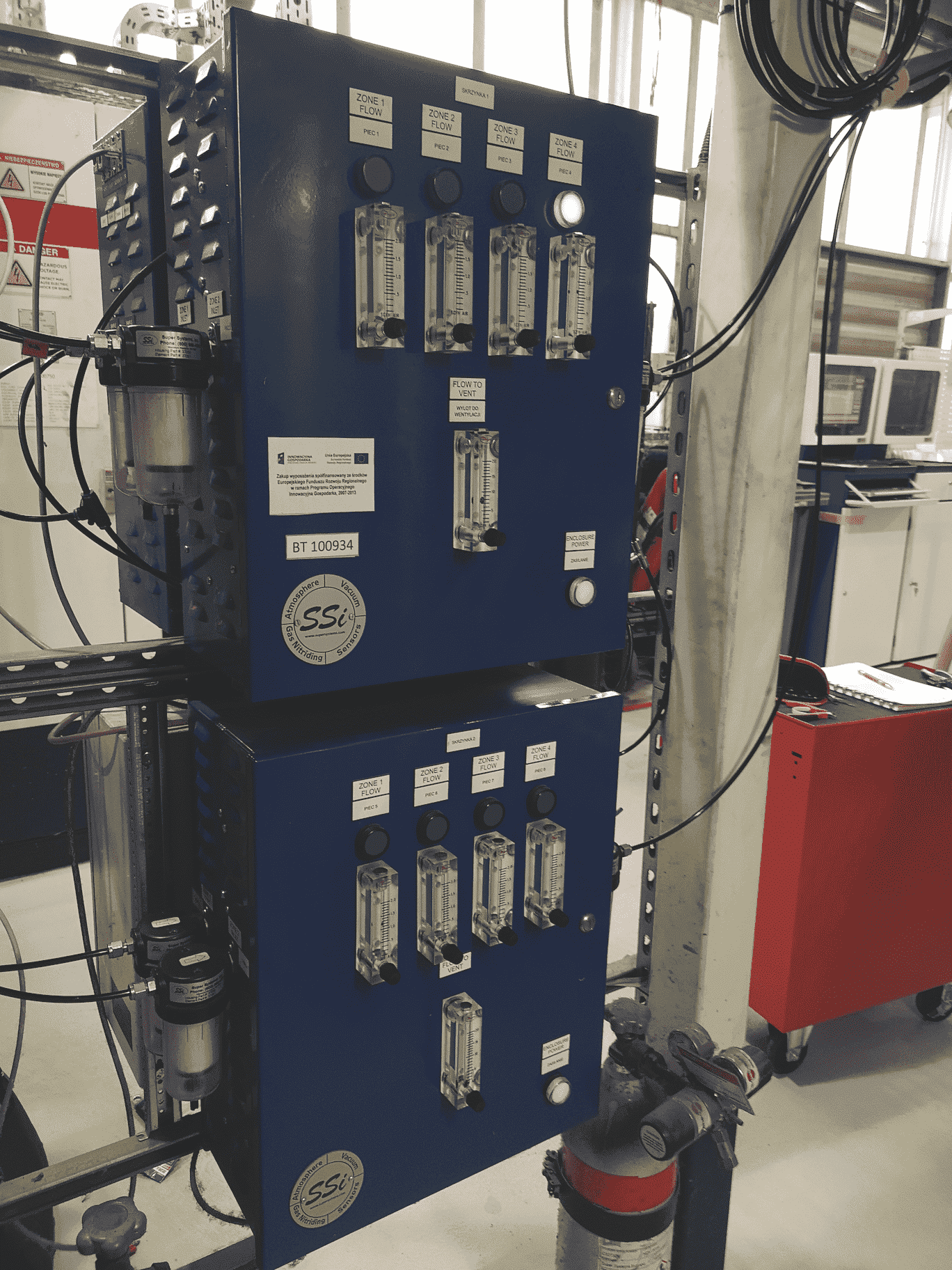
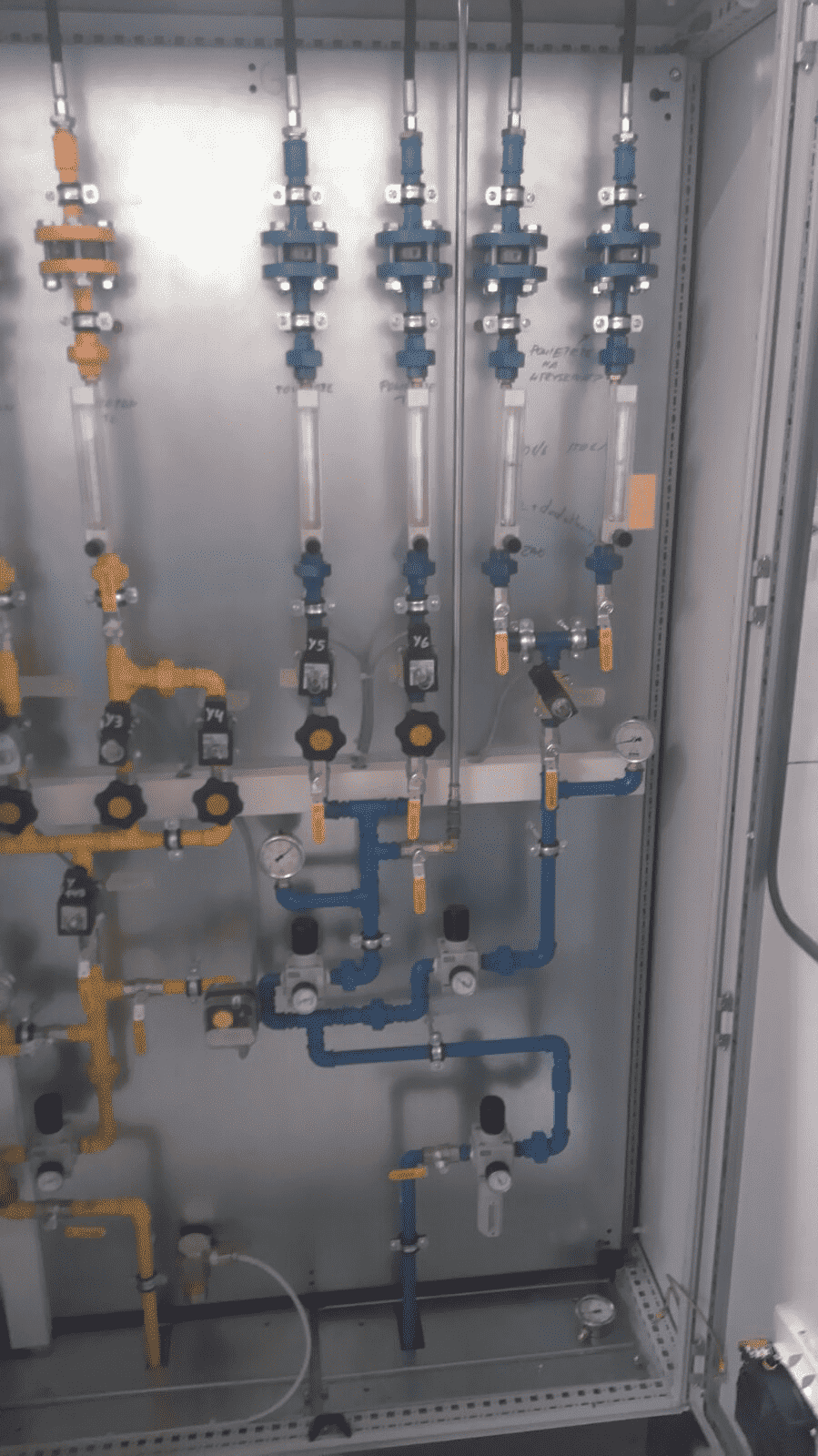
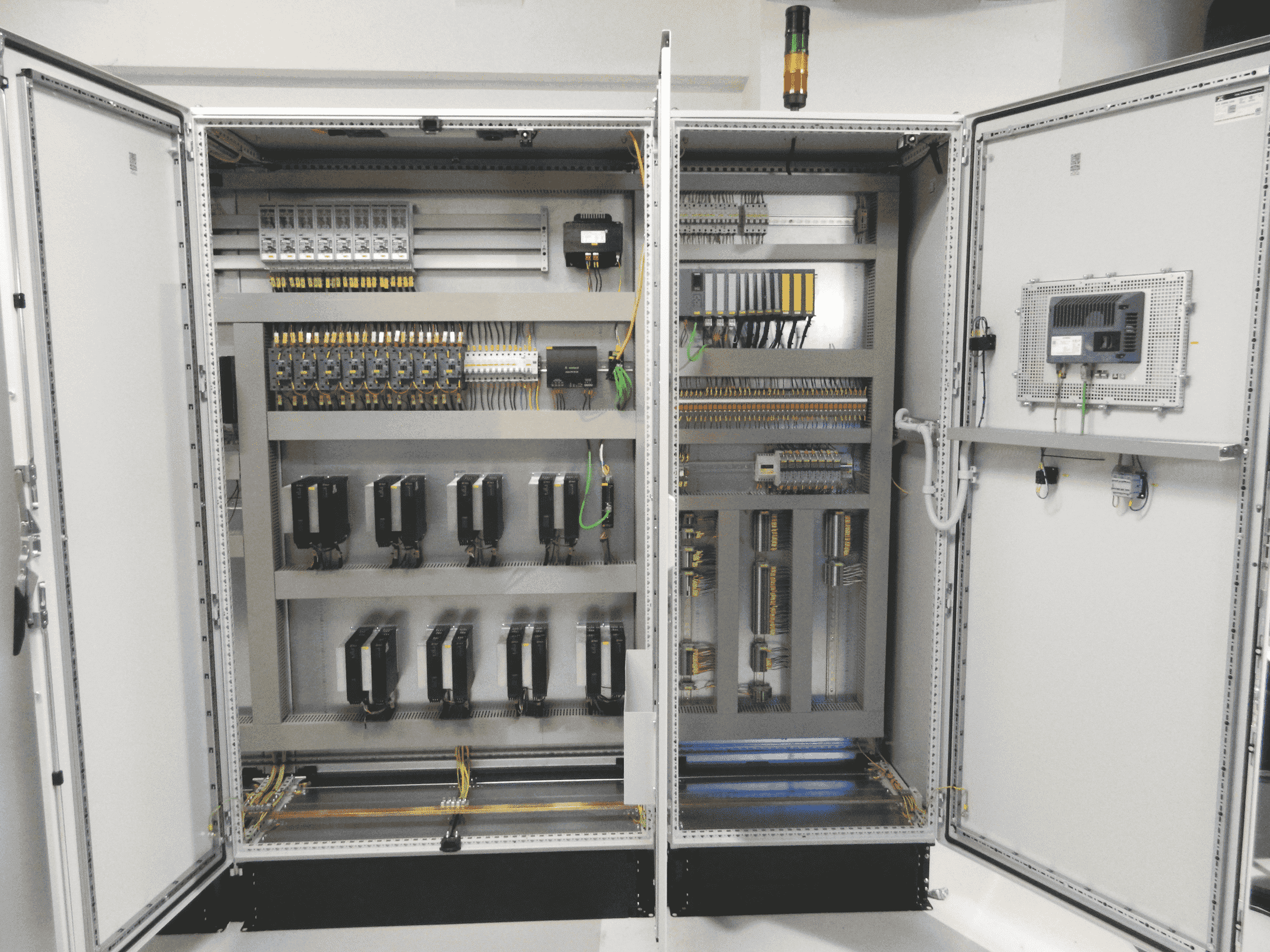
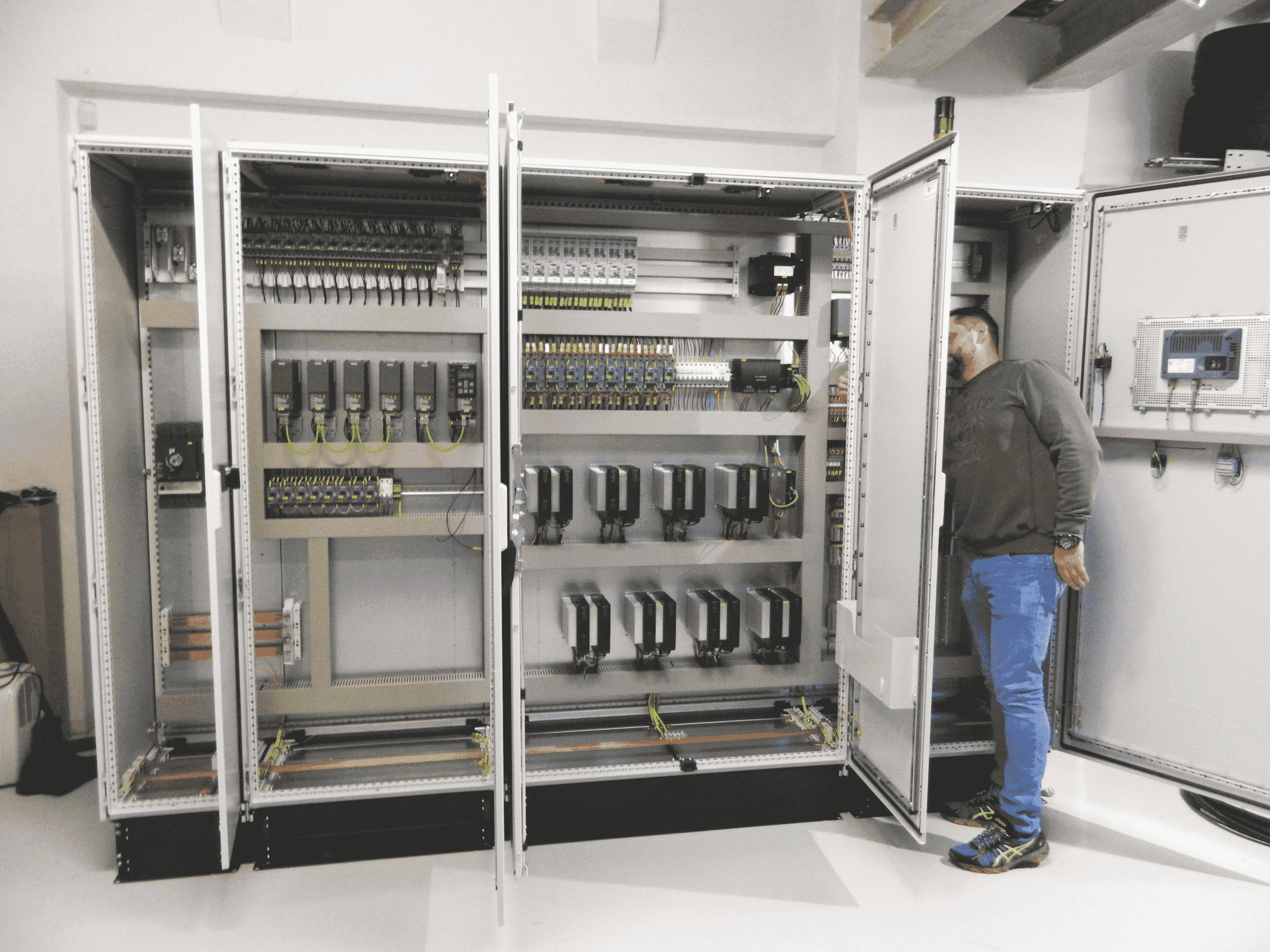
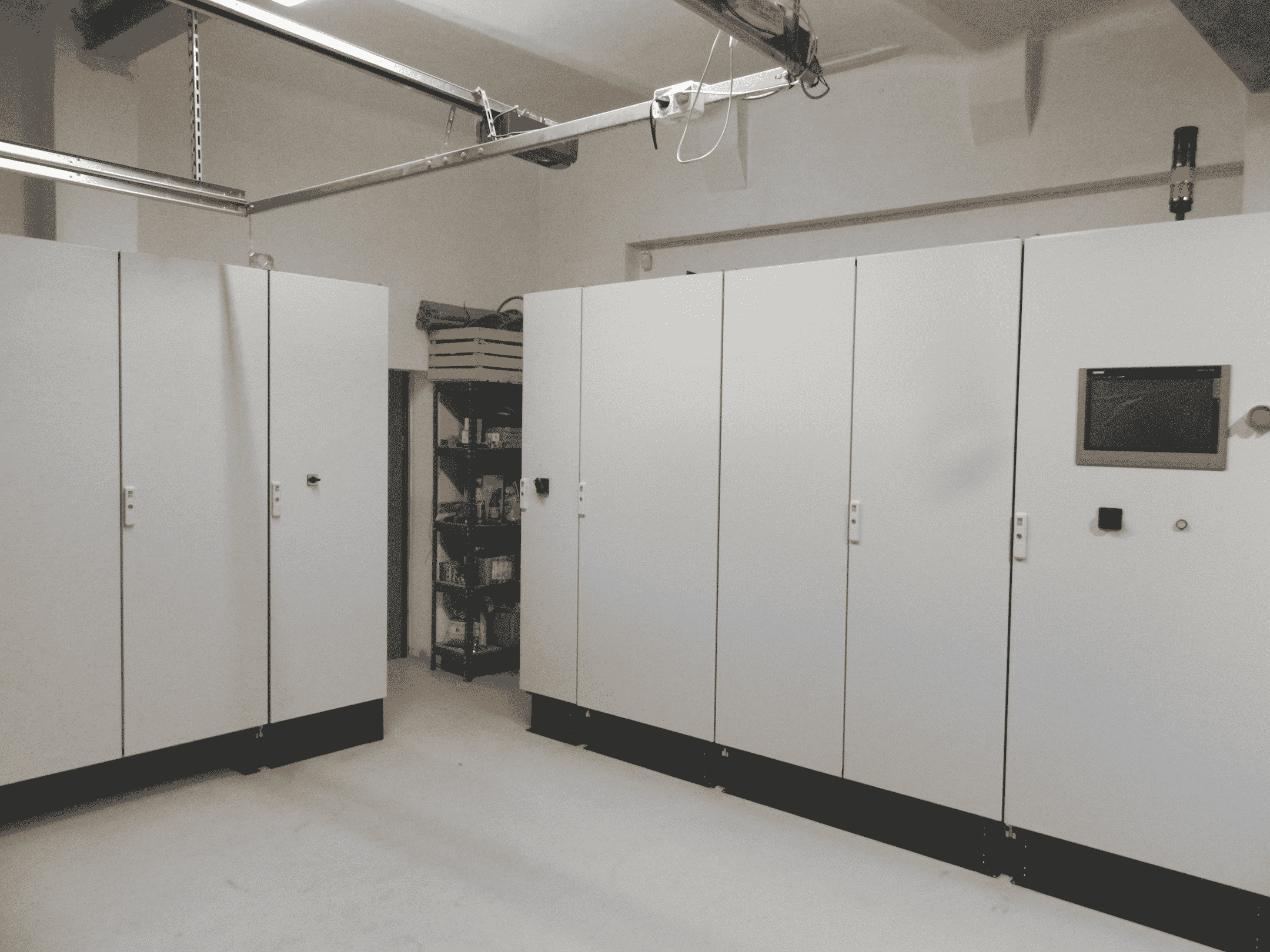
Control and switch cabinet construction
Modernization and complete rebuilding of control cabinets is handled by AVION Europe with its own skilled personnel and high-performance partners. The conversion from S 5 to S 7 control systems is just as much part of the portfolio as the integration of other manufacturers’ control systems in industrial furnace construction.
Here, too, a comprehensive consulting service in advance is the guarantee for trouble-free operation.
- Complete control cabinets and control systems for industrial furnaces, heat treatment lines and auxiliary equipment
- Designed and built based on the latest proven components available on the market (Siemens, Eaton, AEG, Rittal …).
- Modern PLC controls and software based on many years of experience in the heat treatment industry
- Carbon potential, temperature and many other process control parameters integrated in Siemens PLC software (no additional controllers required)
- PLC software built on self-designed ready PLC blocks, which have already proven themselves many times in production.
- For electric or gas-fired furnaces (latest application for over 100-burner furnaces)
- Easy integration into existing SCADA systems
- E-plan documentation and electrical schematics
- Full service including installation, cabling, commissioning, testing and acceptance procedures.
Handling: User-friendly
- SCADA system based on Siemens WinCC for individual furnaces or complete hardening shops
- Full integration with PLC software
- Available communication and information exchange option with other systems (warehouse, quality, gas consumption,…)
- Custom interface and graphics
- Easy identification of faults, alarms, integrated with electrical schematics and PLC alarms.
- Custom reports for customers
- User-defined database for products, customers, orders, process recipes
- Easy integration into the local network
- Online support
Various system structures:
-
Single Station – one computer with one WinCC V7 application
-
Operation from a single PC
-
Cost-effective
-
Not recommended for 24/7 production mode
-
-
Two computers work together as MASTER SLAVE together.
-
High availability for 24/7 systems
-
Redundant system. More than a stand-alone control panel
-
Optionally possible with further redundancy, on local or virtual servers
-
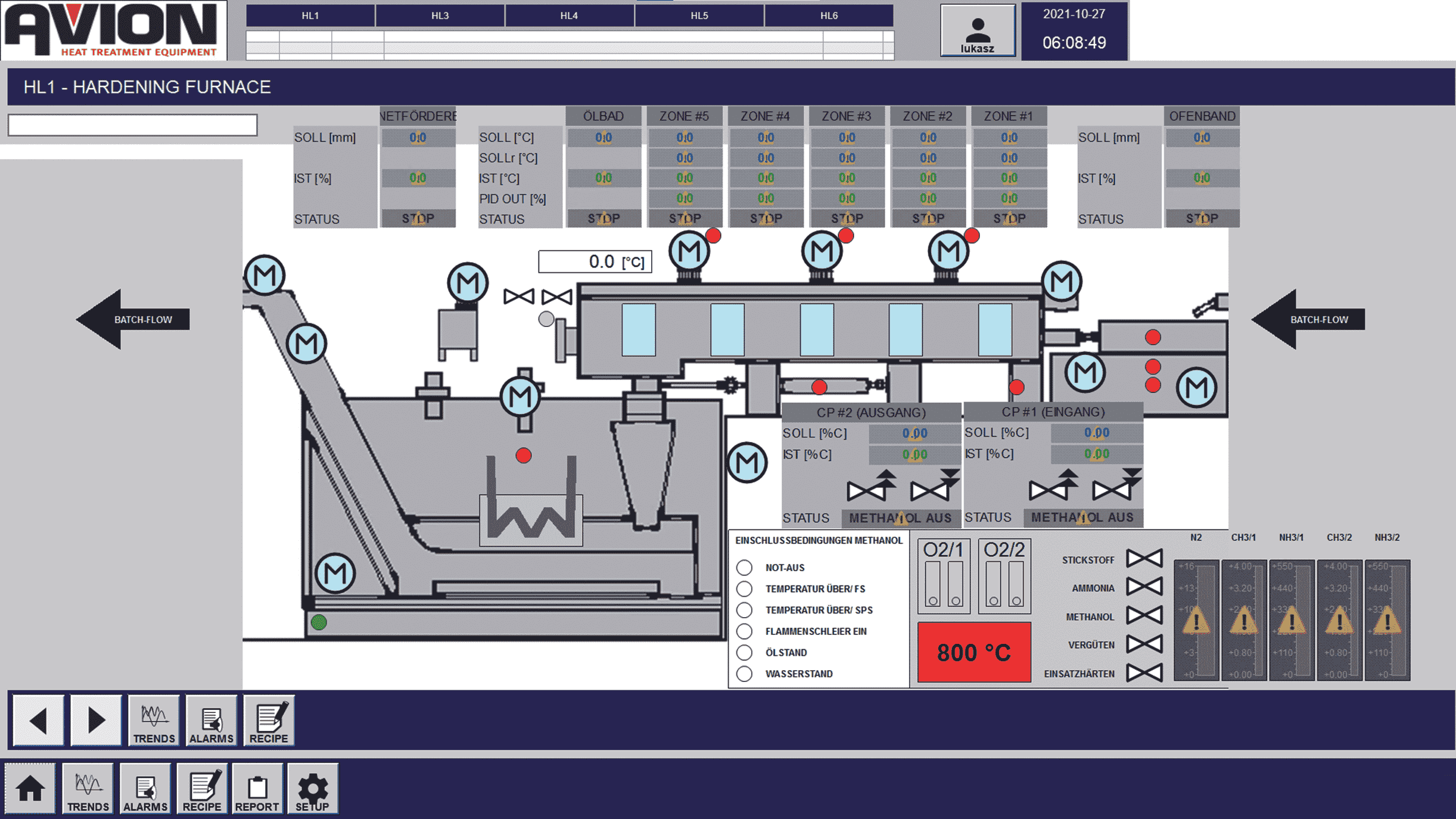
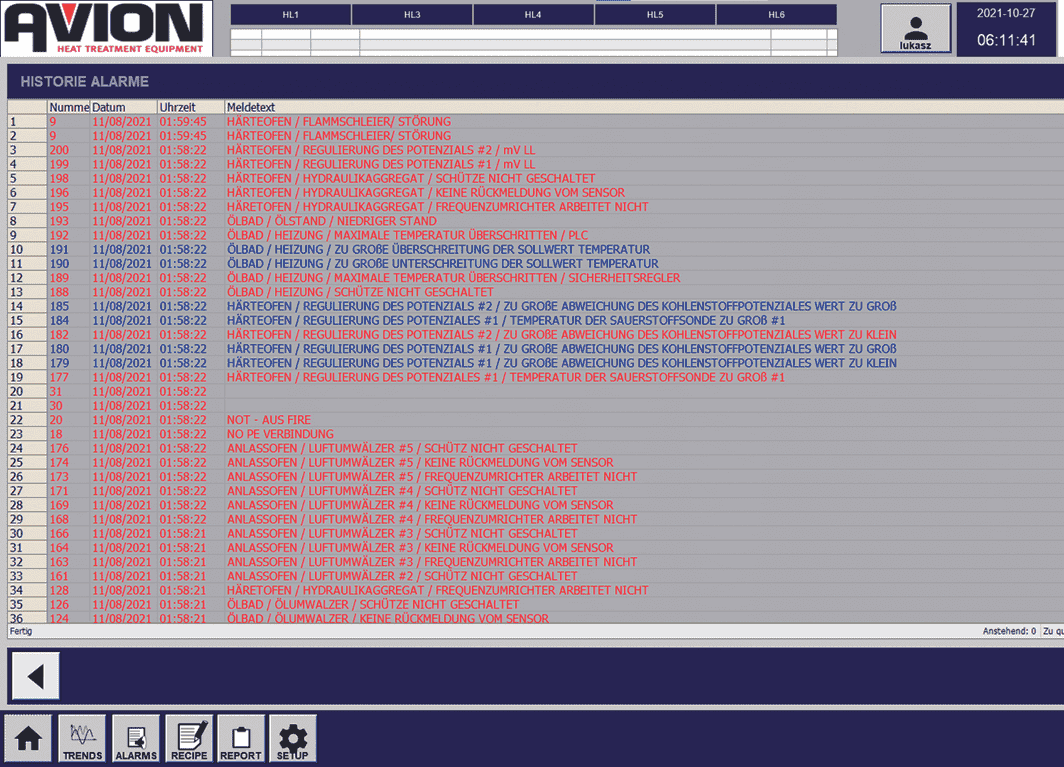
The SCADA system
The construction of individual SCADA (Super-visory Control and Data Acquisition) systems is the new flagship of AVION Europe’s service portfolio. Our customers use SCADA systems to control their plants across sites, and to collect and record data about their operations.
AVION Europe’s SCADA systems, which are individually tailored to our customers, usually include a combination of software and hardware elements, such as programmable logic controllers (PLCs) and remote control terminals (RTUs). Data collection begins with the production equipment at the plant level, which communicates with the manufacturing equipment via sensors.
The data collected in this way is then transmitted to the next level, such as a control station, where operators can monitor the PLC and RTU controls using human-machine interfaces (HMI). AVION Europe SCADA systems allow operators and higher-level interfaces (QA, production management…) to control processes either locally or remotely, as well as to interact directly or centrally with all components such as motors, pumps and sensors.
In addition, AVION Europa SCADA systems enable our customers to monitor, document and archive their processes using real-time data.
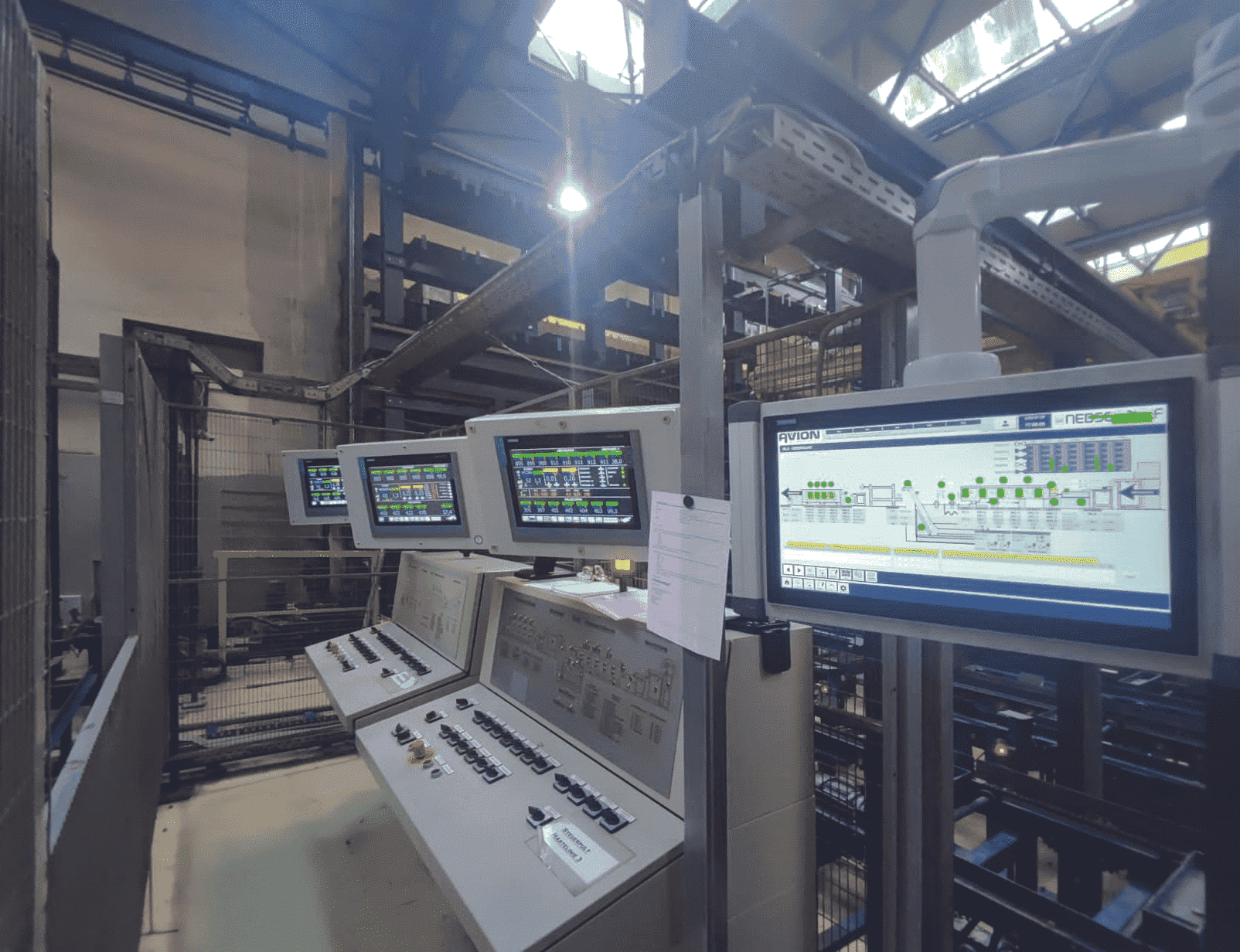
AVION SCADA – Process Monitoring and Protocol System for Heat Treatment Plants
Trends:
- Actual SP, PV values
- User-defined filters (e.g. hardening, tempering)
- History up to 5 years
- Print as .pdf
- Export data in CSV format
Safety Integraion:
- Up to 128 user groups (e.g. administrators, maintenance, technical, operators)
- Each component permission in the application can be defined
- Create, modify and delete users during the entire period of use
- Domain authorization option
Integrations:
- SQL: WinCC system can send data to an external SQL server
- MES/ERP: WinCC V7 offers possibilities for integration with MES/ERP
- QS STAT: Export data in Q-DAS qs-STAT format
- MS Excel: Export data to MS Excel
- Visualization: WinCC V7 can work as a virtual environment
Parameters & PID:
- PID parameter
- Correction parameters
- Authorization for technology group
- Input parameters with constraints (min / max)
Compatible with CQI-9
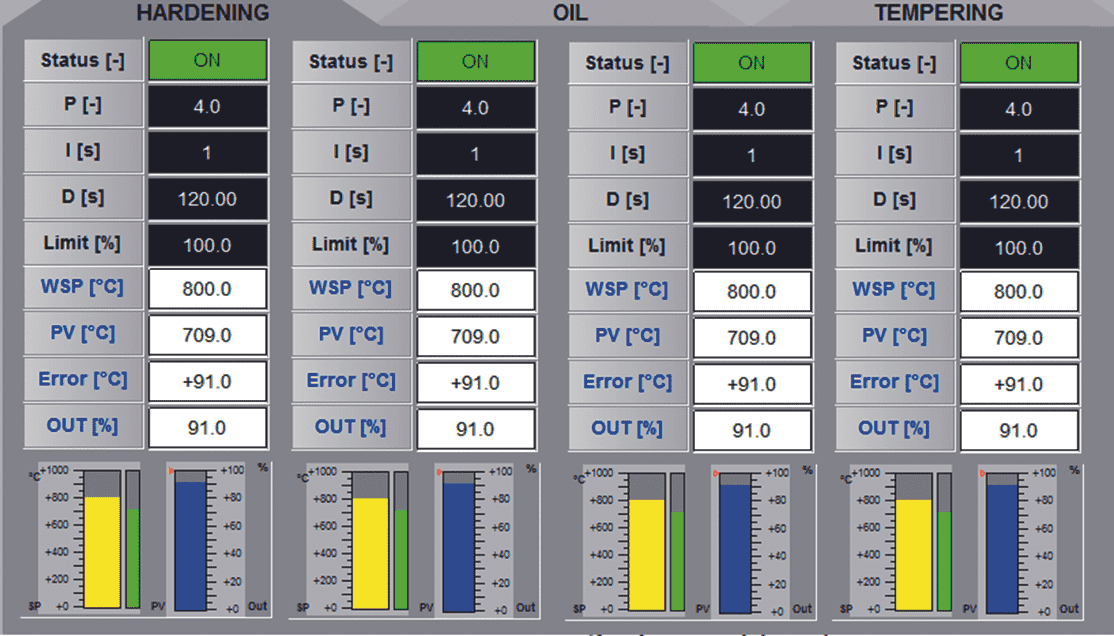
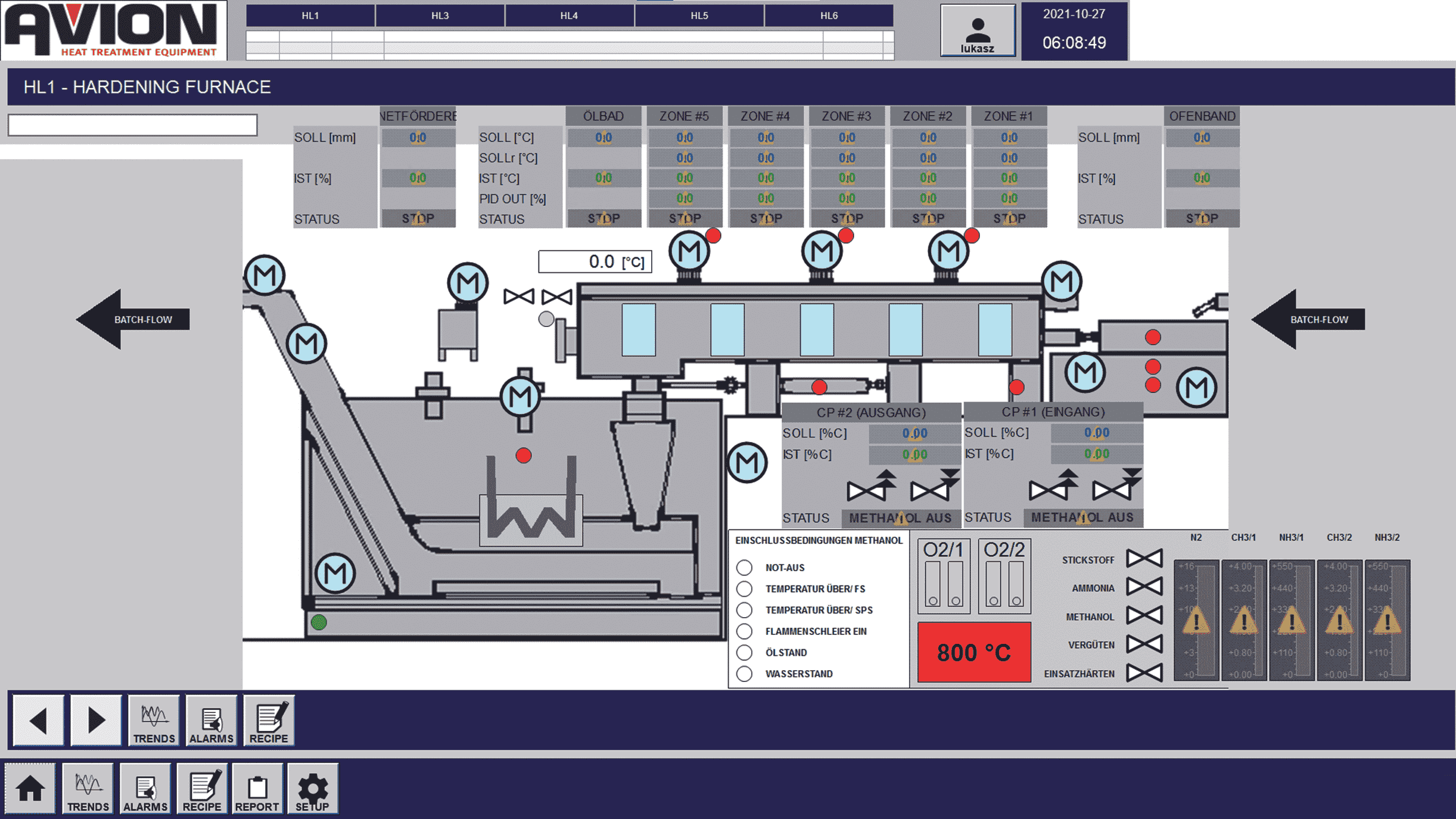
SCADA in use

SCADA the system and its advantages
Graphic system:
- Analog process values
- SP Program
- Displays alarms, warnings
- Events in the process status overview window (complete line)
- Each part of the system (e.g. hardening, tempering, oil, water) has its own window for displaying the respective status
- Menu system for operation
- More than one display language for the operation
Process programs
- Create:
1,000 programs can be created in SCADA - Extinguish:
Operator can delete old programs - To edit:
Operator can open and change programs - Send:
The operator can transfer the program to the PLC - To print:
Operator can print programs as .pdf file
Processing reports
- Predefined reports
- Time stamp for each machine/plant
- Trends for each process (SP, PV
- Process information approach
- Print as .pdf
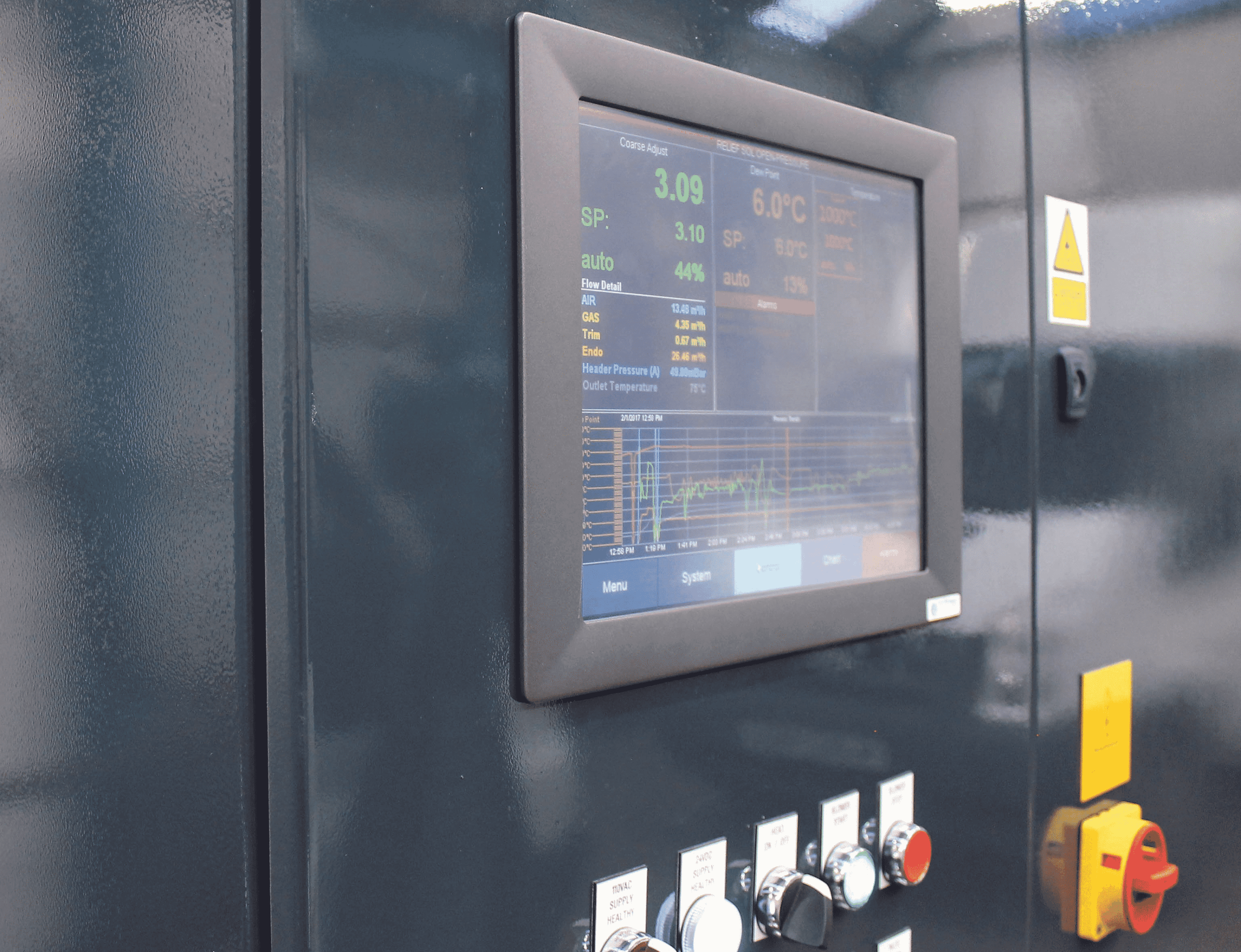
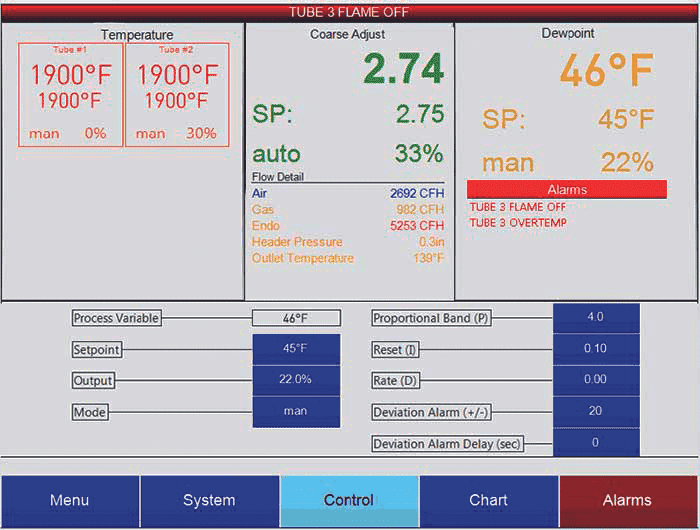

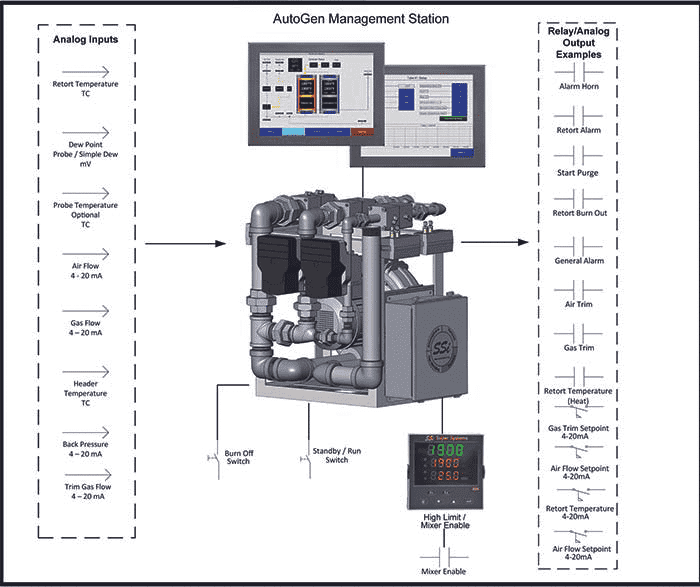
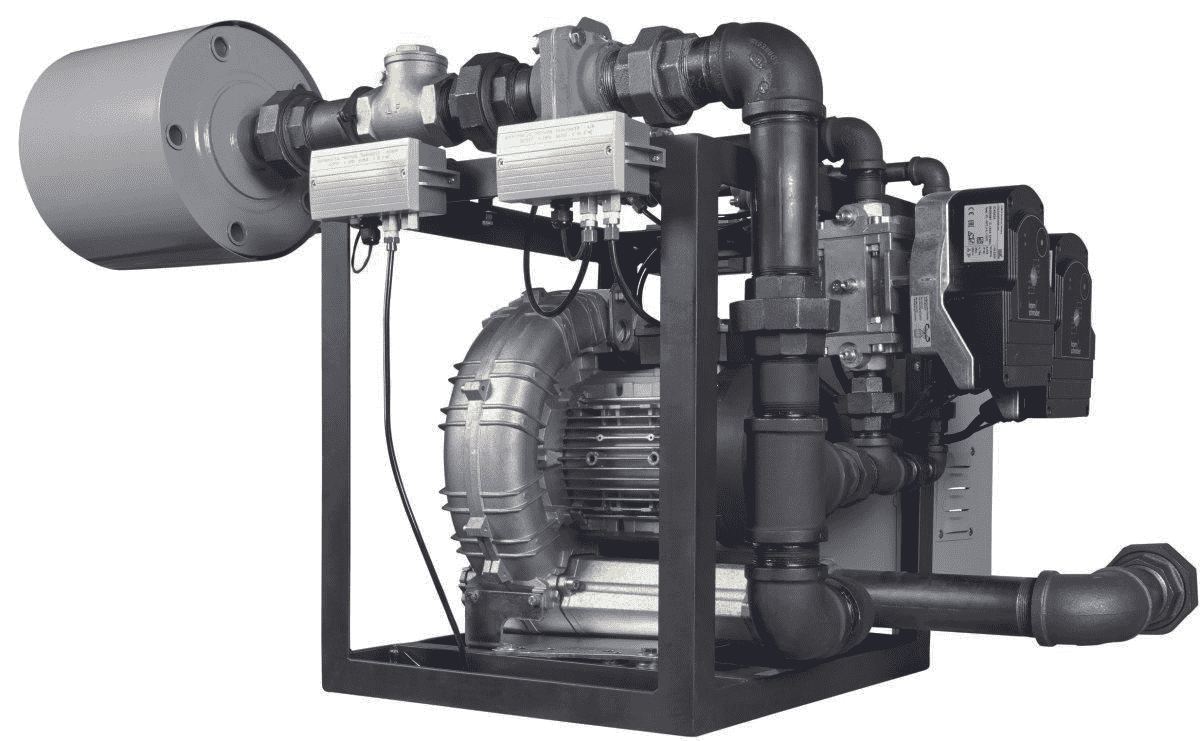
AUTOGEN – control system for endogas generators
The AUTOGEN is a precision gas mixing and control system for endogas generators.
The system features a patented control that uses electronic flow measurement and precise ratio control to consistently deliver the ideal gas mixture for high-quality endogas production.
The AUTOGEN significantly lowers the operating costs, since up to a gas/air ratio of 1:5, excess gas no longer needs to be flared off. The type of control ensures that the generator only produces the amount of protective gas that is required for production. Annoying manual fine adjustments are no longer necessary.
Features and benefits:
- no flaring (1:5): Reduction of operating costs
- Significant reduction in CO² emissions
- minimizes maintenance
- Endogas is available immediately after heating up to operating temperature:
- no “running in” of the generator necessary
- Minimizes setup and startup time
- constant control of the gas/air ratio
- Constant regulation of the dew point: less soot formation
- clear display on a color touchscreen
Included in the system
- colored touch screen
- Integrated dew point measurement and control
- integrated temperature measurement and control
- permanent ratio control gas/air mixture
- integrated, digital chart recorder (data storage for 5 years and more)
- electronic air mass meter
- digital quantity display air / natural gas or propane / endogas
- safety route
- air inlet filter
- Frequency converter for stepless control of the blower motor
specifications
-
power meter
110/220 V at 50/60 Hz -
blower power
230/460 V 3 phases -
flow rate
2.8 – 170 m³/h
2.8 – 390 m³/h -
partial load range
5:1 (or greater) -
at least gas pressure
+1.7 N/cm² + 0.34 N/cm² -
Max. gas pressure
5.0 N/cm² -
Max. operating temperatur
85°C -
communication ports
232/485/Ethernet -
protocol
ModbusRTU -
connections
2″ NPT (unless otherwise noted) -
gas types
propane or natural gas
Conversion from endogas to methanol/nitrogen
Conversion natural gas/propane
The continuing price increases for natural gas are leading our customers to consider moving away from endogas as an inert gas and instead back to methanol/nitrogen as an inert gas atmosphere.Methanol and nitrogen have also increased in price, but not to the same extent as natural gas.
Also, at present, the supply chain risk for methanol/nitrogen is much lower than for natural gas.Our control systems rely on the components of SSI Supersystems, which deals exclusively with mixing and measurement systems for different gases. Conversion from natural gas to propane or LPG is also possible at any time with SSI components.
Our specialists with decades of experience in the heat treatment industry will support you competently and actively in your decision and implementation.
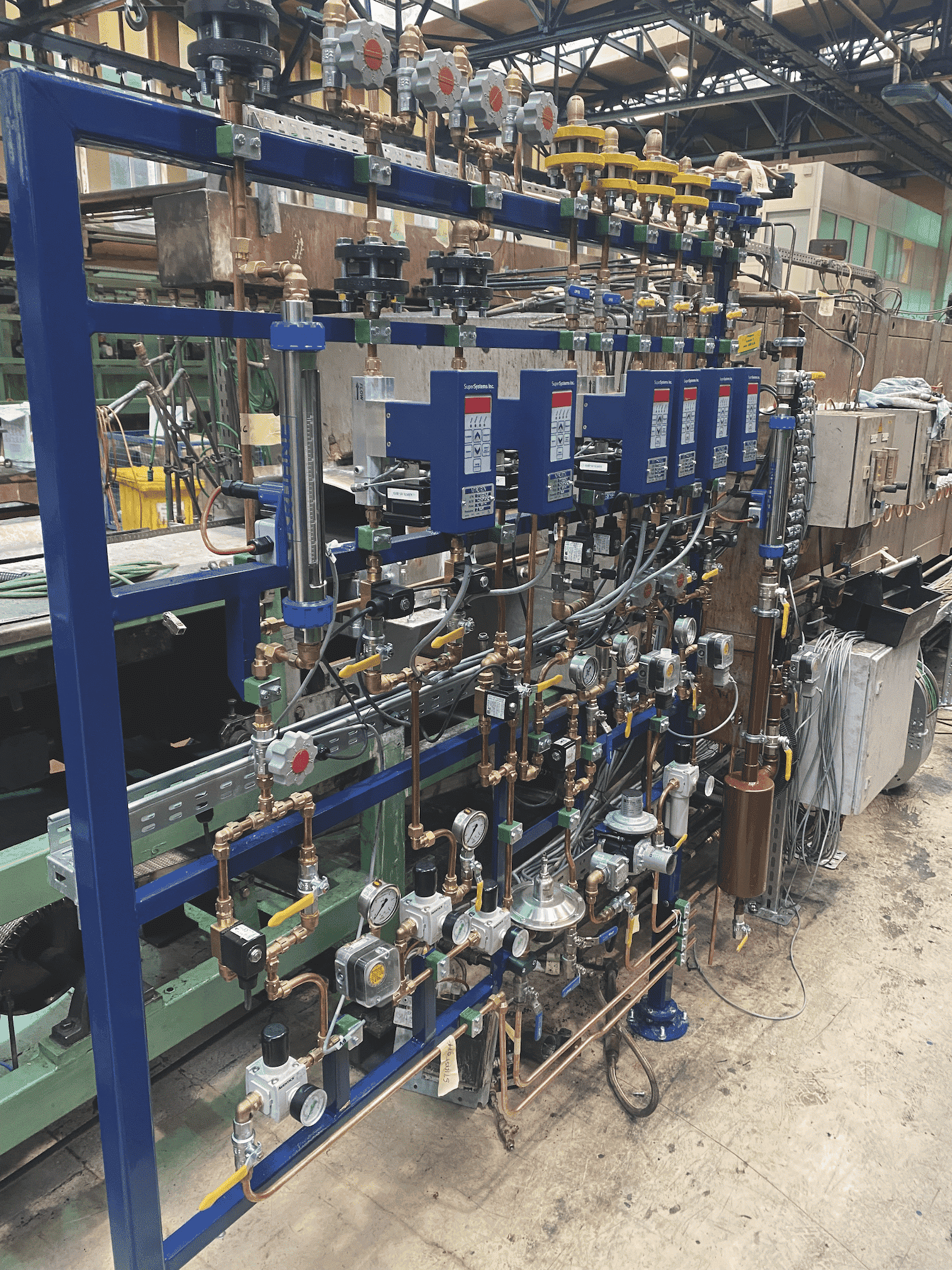
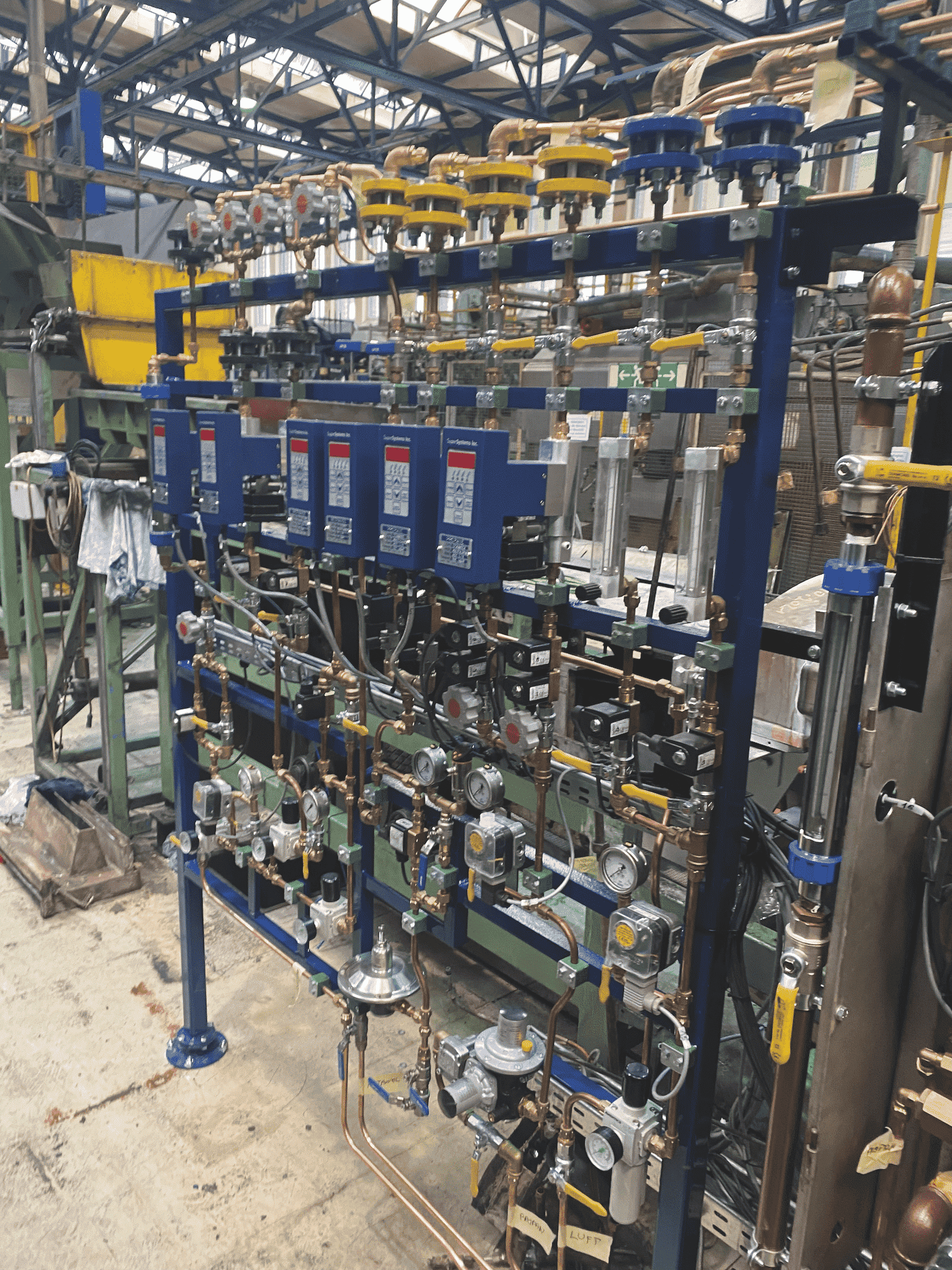